Как записывается серная кислота. Производство серной кислоты
Серную кислоту производят в больших количествах на сернокислотных заводах.
I. Сырьё, используемое для производства серной кислоты:
II. Подготовка сырья.
Разберём производство серной кислоты из пирита FeS 2 .
1) Измельчение пирита.
Перед использованием большие куски пирита измельчают в дробильных машинах. Вы знаете, что при измельчении вещества скорость реакции увеличивается, т.к. увеличивается площадь поверхности соприкосновения реагирующих веществ.
2) Очистка пирита.
После измельчения пирита, его очищают от примесей (пустой породы и земли) методом флотации. Для этого измельчённый пирит опускают в огромные чаны с водой, перемешивают, пустая порода всплывает наверх, затем пустую породу удаляют.
III. Химизм производства.
Производство серной кислоты из пирита состоит из трёх стадий.
![]() |
![]() |
![]() |
|
![]() |
![]() |
![]() |
![]() |
![]() |
![]() |
![]() |
![]() |
![]() |
![]() |
![]() |
![]() |
ПЕРВАЯ СТАДИЯ - обжиг пирита в печи для обжига в "кипящем слое".
Уравнение реакции первой стадии
4FeS 2 + 11O 2 2Fe 2 O 3 + 8SO 2 + Q
Измельчённый очищенный влажный (после флотации) пирит сверху засыпают в печь для обжига в "кипящем слое". Снизу (принцип противотока) пропускают воздух, обогащённый кислородом, для более полного обжига пирита. Температура в печи для обжига достигает 800°С. Пирит раскаляется до красна и находится в "подвешенном состоянии" из-за продуваемого снизу воздуха. Похоже это всё на кипящую жидкость раскалённо-красного цвета.
За счёт выделяющейся теплоты в результате реакции поддерживается температура в печи. Избыточное количество теплоты отводят: по периметру печи проходят трубы с водой, которая нагревается. Горячую воду используют дальше для центрального отопления рядом стоящих помещений.
Образовавшийся оксид железа Fe 2 O 3 (огарок) в производстве серной кислоты не используют. Но его собирают и отправляют на металлургический комбинат, на котором из оксида железа получают металл железо и его сплавы с углеродом - сталь (2% углерода С в сплаве) и чугун (4% углерода С в сплаве).
Таким образом выполняется принцип химического производства - безотходность производства.
Из печи выходит печной газ, состав которого: SO 2 , O 2 , пары воды (пирит был влажный!) и мельчайшие частицы огарка (оксида железа). Такой печной газ необходимо очистить от примесей твёрдых частиц огарка и паров воды.
Очистка печного газа от твёрдых частичек огарка проводят в два этапа - в циклоне (используется центробежная сила, твёрдые частички огарка ударяются о стенки циклона и ссыпаются вниз) и в электрофильтрах (используется электростатическое притяжение, частицы огарка прилипают к наэлектризованным пластинам электрофильтра, при достаточном накоплении под собственной тяжестью они ссыпаются вниз), для удаления паров воды в печном газе (осушка печного газа) используют серную концентрированную кислоту, которая является очень хорошим осушителем, поскольку поглощает воду.
![]() |
Осушку печного газа проводят в сушильной башне - снизу вверх поднимается печной газ, а сверху вниз льётся концентрированная серная кислота. На выходе из сушильной башни печной газ уже не содержит ни частичек огарка, ни паров воды. Печной газ теперь представляет собой смесь оксида серы SO 2 и кислорода О 2 .
ВТОРАЯ СТАДИЯ - окисление SO 2 в SO 3 кислородом.
Протекает в контактном аппарате.
Уравнение реакции этой стадии: 2SO 2 + O 2 2SO 3 + Q
Сложность второй стадии заключается в том, что процесс окисления одного оксида в другой является обратимым. Поэтому необходимо выбрать оптимальные условия протекания прямой реакции (получения SO 3).
![]() |
а) температура:
Прямая реакция является экзотермической +Q, согласно правилам по смещению химического равновесия, для того, чтобы сместить равновесие реакции в сторону экзотермической реакции, температуру в системе необходимо понижать. Но, с другой стороны, при низких температурах, скорость реакции существенно падает. Экспериментальным путём химики-технологи установили, что оптимальной температурой для протекания прямой реакции с максимальным образованием SO 3 является температура 400-500°С. Это достаточно низкая температура в химических производствах. Для того, чтобы увеличить скорость реакции при столь низкой температуре в реакцию вводят катализатор. Экспериментальным путём установили, что наилучшим катализатором для этого процесса является оксид ванадия V 2 O 5 .
б) давление:
Прямая реакция протекает с уменьшением объёмов газов: слева 3V газов (2V SO 2 и 1V O 2), а справа - 2V SO 3 . Раз прямая реакция протекает с уменьшением объёмов газов, то, согласно правилам смещения химического равновесия давление в системе нужно повышать. Поэтому этот процесс проводят при повышенном давлении.
Прежде чем смесь SO 2 и O 2 попадёт в контактный аппарат, её необходимо нагреть до температуры 400-500°С. Нагрев смеси начинается в теплообменнике, который установлен перед контактным аппаратом. Смесь проходит между трубками теплообменника и нагревается от этих трубок. Внутри трубок проходит горячий SO 3 из контактного аппарата. Попадая в контактный аппарат смесь SO 2 и О 2 продолжает нагреваться до нужной температуры, проходя между трубками в контактном аппарате.
Температура 400-500°С в контактном аппарате поддерживается за счёт выделения теплоты в реакции превращения SO 2 в SO 3 . Как только смесь оксида серы и кислорода достигнет слоёв катализатора, начинается процесс окисления SO 2 в SO 3 .
Образовавшийся оксид серы SO 3 выходит из контактного аппарата и через теплообменник попадает в поглотительную башню.
ТРЕТЬЯ СТАДИЯ - поглощение SO 3 серной кислотой.
Протекает в поглотительной башне.
А почему оксид серы SO 3 не поглощают водой? Ведь можно было бы оксид серы растворить в воде: SO 3 + H 2 O H 2 SO 4 . Но дело в том, что если для поглощения оксида серы использовать воду, образуется серная кислота в виде тумана, состоящего из мельчайших капелек серной кислоты (оксид серы растворяется в воде с выделением большого количества теплоты, серная кислота настолько разогревается, что закипает и превращается в пар). Для того, чтобы не образовывалось сернокислотного тумана, используют 98%-ную концентрированную серную кислоту. Два процента воды - это так мало, что нагревание жидкости будет слабым и неопасным. Оксид серы очень хорошо растворяется в такой кислоте, образуя олеум: H 2 SO 4 ·nSO 3 .
Уравнение реакции этого процесса nSO 3 + H 2 SO 4 H 2 SO 4 ·nSO 3
Образовавшийся олеум сливают в металлические резервуары и отправляют на склад. Затем олеумом заполняют цистерны, формируют железнодорожные составы и отправляют потребителю.
Охрана окружающей среды,
связанная с производством серной кислоты.
Основным сырьем для производства серной кислоты, является сера. Она относится к числу наиболее распространенных числу химических элементов на нашей планете.
Производство серной кислоты происходит в три стадии на первой стадии получают SO 2 , путем обжига FeS 2 , затем SO 3 , после чего на третьей стадии получают серную кислоту.
Научно-техническая революция и связанный с ней интенсивный рост химического производства, вызывает существенные негативные изменения в окружающей среде. Например отравление пресных вод, загрязнение земной атмосферы, истребление животных и птиц. В результате мир оказался в тисках экологического кризиса. Вредные выбросы сернокислых заводов следует оценивать не только по действию содержащегося в них оксида серы на расположенные вблизи предприятия зоны, но и учитывать другие факторы - увеличение количества случаев респираторных заболеваний человека и животных, гибель растительности и подавление ее роста, разрушение конструкций из известняка и мрамора, повышение коррозионного износа металлов. По вине “кислых” дождей повреждены памятники архитектуры (Тадж-Макал).
В зоне до 300 км от источника загрязнения (SO 2) опасность представляет серная кислота, в зоне до 600 км. - сульфаты. Серная кислота и сульфаты замедляют рост с/х культур. Закисление водоемов (весной при таянии снега, вызывает гибель икр и молоди рыб. Помимо экологического ущерба налицо экономический ущерб - громадные суммы каждый год теряются при раскисление почв.
Рассмотрим химические метода отчистки от наиболее распространенных газообразных загрязняющих воздух веществ. Известно более 60 методов. Наиболее перспективны методы, основанные на поглощение оксида серы известняком, раствором сульфита - гидросульфита аммония и щелочным раствором алюмината натрия. Интерес также представляют каталитические методы окисления оксида серы в присутствии оксида ванадия.
Особое значение имеет очистка газов от фторсодержащих примесей, которые даже в незначительной концентрации вредно влияют на растительность. Если в газах содержится фтороводород и фтор, то их пропускают через колоны с насадкой противотоком по отношению к 5-10% раствору гидроксида натрия. В течении одной минуты протекают следующие реакции:
F 2 +2NaOH-> O 2 +H 2 O+2NaF
HF+NaOH->NaF+H 2 O;
Образующийся фторид натрия обрабатывают для регенерации гидроксида натрия.
Серную кислоту производят в больших количествах на сернокислотных заводах.
I. Сырьё, используемое для производства серной кислоты:
II. Подготовка сырья.
Разберём производство серной кислоты из пирита FeS 2 .
1) Измельчение пирита.
Перед использованием большие куски пирита измельчают в дробильных машинах. Вы знаете, что при измельчении вещества скорость реакции увеличивается, т.к. увеличивается площадь поверхности соприкосновения реагирующих веществ.
2) Очистка пирита.
После измельчения пирита, его очищают от примесей (пустой породы и земли) методом флотации. Для этого измельчённый пирит опускают в огромные чаны с водой, перемешивают, пустая порода всплывает наверх, затем пустую породу удаляют.
III. Химизм производства.
Производство серной кислоты из пирита состоит из трёх стадий.
![]() |
![]() |
![]() |
|
![]() |
![]() |
![]() |
![]() |
![]() |
![]() |
![]() |
![]() |
![]() |
![]() |
![]() |
![]() |
ПЕРВАЯ СТАДИЯ - обжиг пирита в печи для обжига в "кипящем слое".
Уравнение реакции первой стадии
2Fe 2 O 3 + 8SO 2 + Q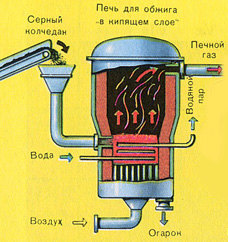
Измельчённый очищенный влажный (после флотации) пирит сверху засыпают в печь для обжига в "кипящем слое". Снизу (принцип противотока) пропускают воздух, обогащённый кислородом, для более полного обжига пирита. Температура в печи для обжига достигает 800°С. Пирит раскаляется до красна и находится в "подвешенном состоянии" из-за продуваемого снизу воздуха. Похоже это всё на кипящую жидкость раскалённо-красного цвета.
За счёт выделяющейся теплоты в результате реакции поддерживается температура в печи. Избыточное количество теплоты отводят: по периметру печи проходят трубы с водой, которая нагревается. Горячую воду используют дальше для центрального отопления рядом стоящих помещений.
Образовавшийся оксид железа Fe 2 O 3 (огарок) в производстве серной кислоты не используют. Но его собирают и отправляют на металлургический комбинат, на котором из оксида железа получают металл железо и его сплавы с углеродом - сталь (2% углерода С в сплаве) и чугун (4% углерода С в сплаве).
Таким образом выполняется принцип химического производства - безотходность производства.
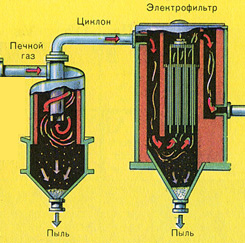
Из печи выходит печной газ, состав которого: SO 2 , O 2 , пары воды (пирит был влажный!) и мельчайшие частицы огарка (оксида железа). Такой печной газ необходимо очистить от примесей твёрдых частиц огарка и паров воды.
Очистка печного газа от твёрдых частичек огарка проводят в два этапа - в циклоне (используется центробежная сила, твёрдые частички огарка ударяются о стенки циклона и ссыпаются вниз) и в электрофильтрах (используется электростатическое притяжение, частицы огарка прилипают к наэлектризованным пластинам электрофильтра, при достаточном накоплении под собственной тяжестью они ссыпаются вниз), для удаления паров воды в печном газе (осушка печного газа) используют серную концентрированную кислоту, которая является очень хорошим осушителем, поскольку поглощает воду.
![]() |
Осушку печного газа проводят в сушильной башне - снизу вверх поднимается печной газ, а сверху вниз льётся концентрированная серная кислота. На выходе из сушильной башни печной газ уже не содержит ни частичек огарка, ни паров воды. Печной газ теперь представляет собой смесь оксида серы SO 2 и кислорода О 2 .
ВТОРАЯ СТАДИЯ - окисление SO 2 в SO 3 кислородом.
Протекает в контактном аппарате.
Уравнение реакции этой стадии: 2SO 2 + O 2
2SO 3 + QСложность второй стадии заключается в том, что процесс окисления одного оксида в другой является обратимым. Поэтому необходимо выбрать оптимальные условия протекания прямой реакции (получения SO 3).
![]() |
а) температура:
Прямая реакция является экзотермической +Q, согласно правилам по смещению химического равновесия, для того, чтобы сместить равновесие реакции в сторону экзотермической реакции, температуру в системе необходимо понижать. Но, с другой стороны, при низких температурах, скорость реакции существенно падает. Экспериментальным путём химики-технологи установили, что оптимальной температурой для протекания прямой реакции с максимальным образованием SO 3 является температура 400-500°С. Это достаточно низкая температура в химических производствах. Для того, чтобы увеличить скорость реакции при столь низкой температуре в реакцию вводят катализатор. Экспериментальным путём установили, что наилучшим катализатором для этого процесса является оксид ванадия V 2 O 5 .
б) давление:
Прямая реакция протекает с уменьшением объёмов газов: слева 3V газов (2V SO 2 и 1V O 2), а справа - 2V SO 3 . Раз прямая реакция протекает с уменьшением объёмов газов, то, согласно правилам смещения химического равновесия давление в системе нужно повышать. Поэтому этот процесс проводят при повышенном давлении.
Прежде чем смесь SO 2 и O 2 попадёт в контактный аппарат, её необходимо нагреть до температуры 400-500°С. Нагрев смеси начинается в теплообменнике, который установлен перед контактным аппаратом. Смесь проходит между трубками теплообменника и нагревается от этих трубок. Внутри трубок проходит горячий SO 3 из контактного аппарата. Попадая в контактный аппарат смесь SO 2 и О 2 продолжает нагреваться до нужной температуры, проходя между трубками в контактном аппарате.
Температура 400-500°С в контактном аппарате поддерживается за счёт выделения теплоты в реакции превращения SO 2 в SO 3 . Как только смесь оксида серы и кислорода достигнет слоёв катализатора, начинается процесс окисления SO 2 в SO 3 .
Образовавшийся оксид серы SO 3 выходит из контактного аппарата и через теплообменник попадает в поглотительную башню.
ТРЕТЬЯ СТАДИЯ - поглощение SO 3 серной кислотой.
Протекает в поглотительной башне.
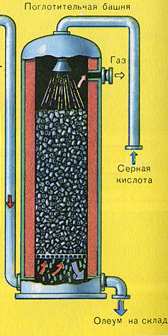
А почему оксид серы SO 3 не поглощают водой? Ведь можно было бы оксид серы растворить в воде: SO 3 + H 2 O
H 2 SO 4 . Но дело в том, что если для поглощения оксида серы использовать воду, образуется серная кислота в виде тумана, состоящего из мельчайших капелек серной кислоты (оксид серы растворяется в воде с выделением большого количества теплоты, серная кислота настолько разогревается, что закипает и превращается в пар). Для того, чтобы не образовывалось сернокислотного тумана, используют 98%-ную концентрированную серную кислоту. Два процента воды - это так мало, что нагревание жидкости будет слабым и неопасным. Оксид серы очень хорошо растворяется в такой кислоте, образуя олеум: H 2 SO 4 ·nSO 3 .Уравнение реакции этого процесса nSO 3 + H 2 SO 4
H 2 SO 4 ·nSO 3Образовавшийся олеум сливают в металлические резервуары и отправляют на склад. Затем олеумом заполняют цистерны, формируют железнодорожные составы и отправляют потребителю.
Охрана окружающей среды,
связанная с производством серной кислоты.
Основным сырьем для производства серной кислоты, является сера. Она относится к числу наиболее распространенных числу химических элементов на нашей планете.
Производство серной кислоты происходит в три стадии на первой стадии получают SO 2 , путем обжига FeS 2 , затем SO 3 , после чего на третьей стадии получают серную кислоту.
Научно-техническая революция и связанный с ней интенсивный рост химического производства, вызывает существенные негативные изменения в окружающей среде. Например отравление пресных вод, загрязнение земной атмосферы, истребление животных и птиц. В результате мир оказался в тисках экологического кризиса. Вредные выбросы сернокислых заводов следует оценивать не только по действию содержащегося в них оксида серы на расположенные вблизи предприятия зоны, но и учитывать другие факторы - увеличение количества случаев респираторных заболеваний человека и животных, гибель растительности и подавление ее роста, разрушение конструкций из известняка и мрамора, повышение коррозионного износа металлов. По вине “кислых” дождей повреждены памятники архитектуры (Тадж-Макал).
В зоне до 300 км от источника загрязнения (SO 2) опасность представляет серная кислота, в зоне до 600 км. - сульфаты. Серная кислота и сульфаты замедляют рост с/х культур. Закисление водоемов (весной при таянии снега, вызывает гибель икр и молоди рыб. Помимо экологического ущерба налицо экономический ущерб - громадные суммы каждый год теряются при раскисление почв.
Рассмотрим химические метода отчистки от наиболее распространенных газообразных загрязняющих воздух веществ. Известно более 60 методов. Наиболее перспективны методы, основанные на поглощение оксида серы известняком, раствором сульфита - гидросульфита аммония и щелочным раствором алюмината натрия. Интерес также представляют каталитические методы окисления оксида серы в присутствии оксида ванадия.
Особое значение имеет очистка газов от фторсодержащих примесей, которые даже в незначительной концентрации вредно влияют на растительность. Если в газах содержится фтороводород и фтор, то их пропускают через колоны с насадкой противотоком по отношению к 5-10% раствору гидроксида натрия. В течении одной минуты протекают следующие реакции:
F 2 +2NaOH-> O 2 +H 2 O+2NaF
HF+NaOH->NaF+H 2 O;
Образующийся фторид натрия обрабатывают для регенерации гидроксида натрия.
Производство кислот
Серная кислота является одним из важнейших продуктов, характеризующий общий уровень развития химической промышленности страны. Объем производства серной кислоты исчисляется десятками миллионов тонн и среди продуктов химической промышленности она по праву занимает первое место. Это объясняется ее широким использованием в различных отраслях промышленности. Серная кислота одна из самых сильных минеральных кислот и самая дешевая. Самый крупный ее потребитель – производство минеральных удобрений (≈41% вырабатываемой в России кислоты): она необходима для получения двойного суперфосфата, фосфорной кислоты и сульфата аммония.
Другие области применения серной кислоты: нефтепереработка, производство синтетических волокон, металлургия, производство красителей и пигментов, текстильная и кожевенная промышленности, гальваника, производство взрывчатых веществ и т.д.
Исходным веществом для производства серной кислоты является сернистый ангидрид SO 2 , который образуется в результате сжигания серы или серосодержащего сырья. Переработка сернистого ангидрида в серную кислоту включает обязательное его окисление до серного ангидрида и последующую адсорбцию его водой.
SO 2 +1/2O 2 +H 2 O→H 2 SO 4
Скорость взаимодействия сернистого ангидрида с кислородом в обычных условиях очень мала, поэтому в промышленности эту реакцию проводят:
1. Контактным методом – это окисление SO 2 кислородом на катализаторе
2. Нитрозным методом окисления с помощью оксидов азота, содержащихся в серной кислоте.
В настоящее время контактным методом получают более 80% всего объема серной кислоты и олеума.
Серную кислоту получают уже более 1000 лет.
Первое упоминание о серной кислоте обнаружено в сочинениях персидского алхимика в 940 году.
В 13 веке серную кислоту получали алхимики из «зеленого камня» (железный купорос) или квасцов путем сильного нагревания (прокаливания). Так, например, из железного купороса получали тяжелую маслянистую жидкость – купоросное масло:
2(FeSO 4 ´7Н 2 O) = Fe 2 O 3 + Н 2 SO 4 + SO 2 + 13Н 2 O.
Первое упоминание о кислых газах, получаемых при прокаливании квасцов или купороса, встречается в сочинениях, приписываемых арабскому алхимику Джафар аль-Суфи (Гебер), жившему в VIII в. Некоторые ученые приписывают честь открытия серной кислоты персидскому алхимику Абубекеру аль-Рази, жившему в Х в. Более определенно говорит о серной кислоте алхимик Альберт Великий.
В 15 веке серную кислоту получали совместным сжиганием серы и селитры в сосудах большого объема, стенки которого смачивали водой. Этим способом ее и получали более 300 лет, но небольшими количествами в ретортах – стеклянных колбах.
Таким способом получали кислоту на первом промышленном заводе в Англии. Сжигали в металлических сосудах, а выделяющиеся газы поглощали водой в другом аппарате – стеклянном.
И только в середине XVIII в. (в 1746гю), когда обнаружили, что свинец является материалом весьма стойким против серной кислоты, стали постепенно переходить от стеклянной лабораторной аппаратуры к большим свинцовым коробкам или камерам, отчего пошло название – камерный способ.. В них сжигалась смесь серы и селитры. Образовавшийся оксид серы(VI) SO 3 здесь же поглощался водой или раствором кислоты, налитой в камеры. Процесс приходилось прерывать для загрузки камер.
Контактный метод возник в 1831г. когда англичанин Филипс предложил окислять SO 2 кислородом, пропуская через раскаленный платиновый катализатор.
Промышленное производство серной кислоты получило быстрое развитие в начале XIX в. Этот рост был вызван развитием производства соды и других продуктов, для которых была необходима серная кислота. В это время химики Н. Клеман и Ш. Б. Дезорм выяснили сущность процесса. Они показали, что оксиды азота играют роль передатчиков кислорода воздуха диоксиду серы, и предложили питать камеры непрерывным током сернистого газа SO 2 , для чего стали сжигать серу в отдельных печах. Вместо селитры употребляли азотную кислоту. Кроме того, в камеры вводили водяной пар. Производство стало непрерывным, однако кислота обходилась дорого до тех пор, пока единственным сырьем для него была сера, а расход азотной кислоты был велик, т.к. оксиды азота безвозвратно терялись с отходящими газами.
Рис. 1 Установка для получения серной кислоты сжиганием серы в присутствии селитры, XVIII в.: 1 – печь, разогреваемая углями; 2 – стеклянный сосуд, где образующиеся газы взаимодействуют с парами воды; 3 – колбы, в которые собирают олеум
Дальнейшие работы химиков устранили эти недостатки. Ж.Л.Гей-Люссак предложил улавливать оксиды азота при помощи серной кислоты, стекающей в установленную после камер башню навстречу отходящим газам.
Получающуюся в башнях кислоту называют нитрозой. Английский технолог Дж. Гловер предложил выделять оксиды азота из нитрозы в башне, в которой навстречу кислоте проходят газы обжига. Эту башню ставят перед камерами. Оксиды азота поступают в камеры, и таким образом совершается их круговорот. Таким образом, осуществлялся нитрозный способ (оксиды азота выделялись за счет разложения селитры).
Еще в XV–XVI вв. извлекать серу умели из пирита FeS 2 – более дешевого и распространенного сырья, чем сера. В 1833 г. было предложено использовать этот минерал для получения из него сернистого газа и построить для этой цели специальную печь.
Благодаря всем этим усовершенствованиям серная кислота стала дешевым продуктом.
Серная кислота
H 2 SO 4 , молярная масса 98,082; бесцветная маслянистая без запаха. Очень сильная двухосновная кислота, при 18°С pK a
1 - 2,8, K 2 1,2·10 -2 , pK a
2 1,92; длины связей в S=O 0,143 нм, S-ОН 0,154 нм, угол HOSOH 104°, OSO 119°; кипит с разложением, образуя (98,3% H 2 SO 4 и 1,7% Н 2 О с температурой кипения 338,8°С; см. также табл. 1). Серная кислота
, отвечающая 100%-ному содержанию H 2 SO 4 , имеет состав (%): H 2 SO 4 99,5%, HSO 4 - 0,18%, H 3 SO 4 + 0,14%, H 3 О + 0,09%, H 2 S 2 O 7 0,04%, HS 2 O 7 0,05%. Смешивается с и SO 3 во всех соотношениях. В водных растворах серная кислота
практически полностью диссоциирует на Н + , HSO 4 - и SO 4 2- . Образует H 2 SO 4 ·n
H 2 O, где n
=1, 2, 3, 4 и 6,5.
растворы SO 3 в серной кислоте называются олеумом, они образуют два соединения H 2 SO 4 ·SO 3 и H 2 SO 4 ·2SO 3 . Олеум содержит также пиросерную кислоту, получающуюся по реакции: Н 2 SO 4 +SO 3 =H 2 S 2 O 7 .
Получение серной кислоты
Сырьем для получения серной кислоты
служат: S, сульфиды металлов, H 2 S, отходящие теплоэлектростанций, сульфаты Fe, Ca и др. Основные стадии получения серной кислоты
: 1) сырья с получением SO 2 ; 2) SO 2 до SO 3 (конверсия); 3) SO 3 . В промышленности применяют два метода получения серной кислоты
, отличающихся способом окисления SO 2 , - контактный с использованием твердых катализаторов (контактов) и нитрозный - с оксидами азота. Для получения серной кислоты
контактным способом на современных заводах применяют ванадиевые катализаторы, вытеснившие Pt и оксиды Fe. Чистый V 2 O 5 обладает слабой каталитической активностью, резко возрастающей в присутствии щелочных металлов, причем наибольшее влияние оказывают соли К. Промотирующая роль щелочных металлов обусловлена образованием низкоплавких пиросульфованадатов (3К 2 S 2 О 7 · V 2 О 5 , 2К 2 S 2 O 7 · V 2 O 5 и K 2 S 2 O 7 ·V 2 O 5 , разлагающихся соответственно при 315-330, 365-380 и 400-405 °С). Активный компонент в условиях катализа находится в расплавленном состоянии.
Схему окисления SO 2 в SO 3 можно представить следующим образом:
На первой стадии достигается равновесие, вторая стадия медленная и определяет скорость процесса.
Производство серной кислоты
из серы по методу двойного контактирования и двойной абсорбции (рис. 1) состоит из следующих стадий. Воздух после очистки от пыли подается газодувкой в сушильную башню, где он осушается 93-98%-ной серной кислотой
до содержания влаги 0,01% по объему. Осушенный воздух поступает в серную печь после предварительного подогрева в одном из теплообменников контактного узла. В печи сжигается сера, подаваемая форсунками: S + О 2 = SO 2 + 297,028 кДж. Газ, содержащий 10-14% по объему SO 2 , охлаждается в котле и после разбавления воздухом до содержания SO 2 9-10% по объему при 420°С поступает в контактный аппарат на первую стадию конверсии, которая протекает на трех слоях катализатора (SO 2 + V 2 O 2 = SO 3 + 96,296 кДж), после чего газ охлаждается в теплообменниках. Затем газ, содержащий 8,5-9,5% SO 3 , при 200°С поступает на первую стадию абсорбции в абсорбер, орошаемый и 98%-ной серной кислотой
: SO 3 + Н 2 О = Н 2 SO 4 + 130,56 кДж. Далее газ проходит очистку от брызг серной кислоты
, нагревается до 420°С и поступает на вторую стадию конверсии, протекающую на двух слоях катализатора. Перед второй стадией абсорбции газ охлаждается в экономайзере и подается в абсорбер второй ступени, орошаемый 98%-ной серной кислотой
, и затем после очистки от брызг выбрасывается в атмосферу.
1 - серная печь; 2 - котел-утилизатор; 3 - экономайзер; 4 - пусковая топка; 5, 6 - теплообменники пусковой топки; 7 - контактный аппарат; 8 - теплообменники; 9 - олеумный абсорбер; 10 - сушильная башня; 11 и 12 - соответственно первый и второй моногидратные абсорберы; 13 - сборники кислоты.
1 - тарельчатый питатель; 2 - печь; 3 - котел-утилизатор; 4 - циклоны; 5 - электрофильтры; 6 - промывные башни; 7 - мокрые электрофильтры; 8 - отдувочная башня; 9 - сушильная башня; 10 - брызгоуловитель; 11 - первый моногидратный абсорбер; 12 - теплообменники; 13 - контактный аппарат; 14 - олеумный абсорбер; 15 - второй моногидратный абсорбер; 16 - холодильники; 17 - сборники.
1 - денитрационная башня; 2, 3 - первая и вторая продукционные башни; 4 - окислительная башня; 5, 6, 7 - абсорбционные башни; 8 - электрофильтры.
Производство серной кислоты
из сульфидов металлов (рис. 2) существенно сложнее и состоит из следующих операций. Обжиг FeS 2 производят в печи кипящего слоя на воздушном дутье: 4FeS 2 + 11О 2 = 2Fe 2 O 3 + 8SO 2 + 13476 кДж. Обжиговый газ с содержанием SO 2 13-14%, имеющий температуру 900°С, поступает в котел, где охлаждается до 450°С. Очистку от пыли осуществляют в циклоне и электрофильтре. Далее газ проходит через две промывные башни, орошаемые 40%-ной и 10%-ной серной кислотой
. При этом газ окончательно очищается от пыли, фтора и мышьяка. Для очистки газа от аэрозоля серной кислоты
, образующегося в промывных башнях, предусмотрены две ступени мокрых электрофильтров. После осушки в сушильной башне, перед которой газ разбавляется до содержания 9% SO 2 , его газодувкой подают на первую стадию конверсии (3 слоя катализатора). В теплообменниках газ подогревается до 420°С благодаря теплу газа, поступающего с первой стадии конверсии. SO 2 , окисленный на 92-95% в SO 3 , идет на первую стадию абсорбции в олеумный и моногидратный абсорберы, где освобождается от SO 3 . Далее газ с содержанием SO 2 ~ 0,5% поступает на вторую стадию конверсии, которая протекает на одном или двух слоях катализатора. Предварительно газ нагревается в другой группе теплообменников до420 °С благодаря теплу газов, идущих со второй стадии катализа. После отделения SO 3 на второй стадии абсорбции газ выбрасывается в атмосферу.
Степень превращения SO 2 в SO 3 при контактном способе 99,7%, степень абсорбции SO 3 99,97%. Производство серной кислоты
осуществляют и в одну стадию катализа, при этом степень превращения SO 2 в SO 3 не превышает 98,5%. Перед выбросом в атмосферу газ очищают от оставшегося SO 2 (см. ). Производительность современных установок 1500-3100 т/сут.
Сущность нитрозного метода (рис. 3) состоит в том, что обжиговый газ после охлаждения и очистки от пыли обрабатывают так называемой нитрозой - серной кислотой
, в которой растворены оксиды азота. SO 2 поглощается нитрозой, а затем окисляется: SO 2 + N 2 O 3 + Н 2 О = Н 2 SO 4 + NO. Образующийся NO плохо растворим в нитрозе и выделяется из нее, а затем частично окисляется кислородом в газовой фазе до NO 2 . Смесь NO и NO 2 вновь поглощается серной кислотой
и т.д. Оксиды азота не расходуются в нитрозном процессе и возвращаются в производственный цикл, вследствие неполного поглощения их серной кислотой
они частично уносятся отходящими газами. Достоинства нитрозного метода: простота аппаратурного оформления, более низкая себестоимость (на 10-15% ниже контактной), возможность 100%-ной переработки SO 2 .
Аппаратурное оформление башенного нитрозного процесса несложно: SO 2 перерабатывается в 7-8 футерованных башнях с керамической насадкой, одна из башен (полая) является регулируемым окислительным объемом. Башни имеют сборники кислоты, холодильники, насосы, подающие кислоту в напорные баки над башнями. Перед двумя последними башнями устанавливается хвостовой вентилятор. Для очистки газа от аэрозоля серной кислоты
служит электрофильтр. Оксиды азота, необходимые для процесса, получают из HNO 3 . Для сокращения выброса оксидов азота в атмосферу и 100%-ной переработки SO 2 между продукционной и абсорбционной зонами устанавливается безнитрозный цикл переработки SO 2 в комбинации с водно-кислотным методом глубокого улавливания оксидов азота. Недостаток нитрозного метода - низкое качество продукции: концентрация серной кислоты
75%, наличие оксидов азота, Fe и др. примесей.
Для уменьшения возможности кристаллизации серной кислоты
при перевозке и хранении установлены стандарты на товарные сорта серной кислоты
, концентрация которых соответствует наиболее низким температурам кристаллизации. Содержание серной кислоты
в технических сортах (%): башенная (нитрозная) 75, контактная 92,5-98,0, олеум 104,5, высокопроцентный олеум 114,6, аккумуляторная 92-94. Серную кислоту
хранят в стальных резервуарах объемом до 5000 м 3 , их общая емкость на складе рассчитана на десятисуточньй выпуск продукции. Олеум и серную кислоту
перевозят в стальных железнодорожных цистернах. Концентрированную и аккумуляторную серную кислоту
перевозят в цистернах из кислотостойкой стали. Цистерны для перевозки олеума покрывают теплоизоляцией и перед заливкой олеум подогревают.
Определяют серную кислоту
колориметрически и фотометрически, в виде взвеси BaSO 4 - фототурбидиметрически, а также кулонометрическим методом.
Применение серной кислоты
Серную кислоту применяют в производстве минеральных удобрений, как электролит в свинцовых аккумуляторах, для получения различных минеральных кислот и солей, химических волокон, красителей, дымообразующих веществ и взрывчатых веществ, в нефтяной, металлообрабатывающей, текстильной, кожевенной и др. отраслях промышленности. Ее используют в промышленном органическом синтезе в реакциях дегидратации (получение диэтилового эфира, сложных эфиров), гидратации (этанол из этилена), сульфирования ( и промежуточные продукты в производстве красителей), алкилирования (получение изооктана, полиэтиленгликоля, капролактама) и др. Самый крупный потребитель серной кислоты
- производство минеральных удобрений. На 1 т Р 2 О 5 фосфорных удобрений расходуется 2,2-3,4 т серной кислоты
, а на 1 т (NH 4) 2 SO 4 - 0,75 т серной кислоты
. Поэтому сернокислотные заводы стремятся строить в комплексе с заводами по производству минеральных удобрений. Мировое производство серной кислоты
в 1987 достигло 152 млн. тонн.
Серная кислота и олеум - чрезвычайно агрессивные вещества, поражают дыхательные пути, кожу, слизистые оболочки, вызывают затруднение дыхания, кашель, нередко - ларингит, трахеит, бронхит и т.д. ПДК аэрозоля серной кислоты в воздухе рабочей зоны 1,0 мг/м 3 , в атмосферном 0,3 мг/м 3 (максимальная разовая) и 0,1 мг/м 3 (среднесуточная). Поражающая концентрация паров серной кислоты 0,008 мг/л (экспозиция 60 мин), смертельная 0,18 мг/л (60 мин). Класс опасности 2. Аэрозоль серной кислоты может образовываться в атмосфере в результате выбросов химических и металлургических производств, содержащих оксиды S, и выпадать в виде кислотных дождей.
О промышленном развитии страны можно судить по количеству серной кислоты, которую она потребляет.
Юстус Либих (1803-1873)
Ежегодно производство серной кислоты в мире превышает 100 млн. т. На долю Великобритании приходится менее 3% ее производства - от 3 до 3,5 млн. т в год. Приблизительно 28% этого количества расходуется для нужд сельского хозяйства, включая производство удобрений. На рис. 7.4 показана диаграмма использования серной кислоты в Великобритании в 1981 г.
Рис. 7.4. Использование серной кислоты на различные нужды экономики Великобритании в 1981 г.
Применения серной кислоты
Удобрении. В экономике Великобритании приблизительно 26% всей серной кислоты используется для получения суперфосфатных удобрений (см. разд. 15.3). Еще 2% используется для получения сульфата аммония.
Моющие средства. Натриевые соли сульфонатов неразветвленных алкилбензолов используются в качестве главных активных компонентов бытовых синтетических моющих средств. Серная кислота или олеум используются для производства этих сульфонатов.
Пигменты. Серная кислота используется на первой стадии сульфатного процесса получения оксида Диоксид титана находит применение в качестве пигмента белых красок.
Искусственные ткани. Серная кислота используется для получения капролактама из циклогексанона. Капролактам представляет собой мономер, из которого получают полимер найлон-6.
Современный контактный процесс
В настоящее время серную кислоту во всем мире получают с помощью контактного процесса. Этот процесс включает три стадии.
1-я стадия. На этой стадии получают диоксид серы: жидкую серу разбрызгивают в камере сгорания, где она сгорает в воздухе при температуре порядка 1000 °С:
Воздух, поступающий в камеру, должен быть сухим, чтобы предотвратить образование тумана. Серу получают с помощью процесса Фраша из залежей, расположенных в Польше, Мексике и США (см. разд. 15.4). Свободную серу получают также в качестве побочного продукта при переработке нефти и очистке природного газа. Например, французский или канадский природный газ содержит до 25% сероводорода.
Диоксид серы получают также при обжиге сульфидных минералов, например сульфида цинка или железного колчедана:
Следует отметить, что оба указанных здесь процесса окисления являются необратимыми и экзотермическими.
2-я стадия. На этой стадии получают триоксид серы:
Эта реакция является обратимой и экзотермической. Высокому выходу триоксида серы благоприятствуют низкие температуры и высокие давления. На практике этот процесс проводится при давлении несколько выше атмосферного. Это делается только для того, чтобы обеспечить хороший поток газа. Увеличение выхода в результате повышения давления не оправдывает дополнительных затрат.
Питающий газ (смесь диоксида серы и кислорода) пропускают через каталитический конвертер, который состоит из ряда слоев, содержащих катализатор-оксид и промоторы. Поскольку превращение диоксида серы в триоксид серы является экзотермической реакцией, температура газа повышается. Поэтому газы, выходящие из каждого слоя конвертера, пропускают через теплообменники, где они охлаждаются. Действие теплообменника основано на том же принципе, что и у конденсатора Либиха, используемого в химических лабораториях. После прохождения каждого слоя реактора доля образующегося триоксида серы все возрастает. Температуру каталитических слоев поддерживают на уровне не ниже 400 °С, поскольку при более низких температурах катализатор теряет свою активность. Окончательный выход для конвертера, содержащего четыре каталитических слоя, достигает 98%.
3-я стадия. На этой стадии осуществляется следующий процесс:
Однако непосредственное поглощение триоксида серы водой невозможно, потому что пары воды над ее поверхностью образуют устойчивый туман из крошечных капелек серной кислоты. Поэтому для поглощения триоксида серы используется 98%-ная серная кислота. Ее концентрацию повышают до 99,5% (рис. 7.5). Затем кислоту снова разбавляют водой до 98%. Часть ее возвращают на поглощение, а остальную часть направляют на хранение. Если допустить, чтобы концентрация серной кислоты превысила 99,5%, то давление паров триоксида серы становится слишком высоким, и это препятствует их полному поглощению. В результате образуется видимый туман. Серную кислоту с концентрацией 99,5% иногда называют «олеум» и обозначают формулой
Рис. 7.5. 3-я стадия процесса получения серной кислоты контактным способом (процесс поглощения).
Завод контактной серной кислоты с двойным поглощением
На заводе контактной серной кислоты с однократным поглощением описанные выше процессы протекают в три стадии.
1-я стадия: получение
2-я стадия: 8%-ное превращение
3-я стадия: поглощение в 98%-ной с образованием олеума.
На заводе контактной серной кислоты с двойным поглощением, поглощение происходит на 2-й и 3-й стадиях.
1-я стадия: получение
2-я стадия:
а) превращение
б) поглощение в с образованием олеума - так называемое промежуточное поглощение;
в) превращение оставшегося в результате чего окончательный выход повышается до 99,5%.
(см. скан)
Рис. 7.6. Схема конвертера на заводе по производству серной кислоты контактным способом с двойным поглощением.
3-я стадия: окончательное поглощение в 98%-ной с образованием олеума.
На заводе контактной серной кислоты с двойным поглощением достигается 99,5%-ное превращение диоксида серы в триоксид серы. Это позволяет предельно уменьшить выброс диоксида серы в атмосферу и, следовательно, снизить загрязнение окружающей среды. Минимальная эффективность превращения 99,5% в настоящее время является обязательным требованием для всех строящихся в Великобритании заводов, на которых осуществляется сжигание серы.
На рис. 7.6 показана схема включения промежуточного поглотителя в конвертер на 2-й стадии производства серной кислоты на заводе с двойным поглощением. Питающий газ, который содержит приблизительно 10% диоксида серы и 11% кислорода, впускают в конвертер, где находятся каталитические слои. После прохождения первого слоя достигается 63%-ное превращение диоксида серы в триоксид серы. После прохождения третьего слоя весь триоксид серы удаляется и поглощается на стадии промежуточного поглощения. Непоглотившиеся газы возвращаются в повторный цикл, где они смешиваются с оставшимся диоксидом серы и кислородом для завершающего превращения. Затем триоксид серы, образовавшийся после прохождения четвертого каталитического слоя, поступает в окончательный поглотитель.
Итак, повторим еще раз!
1. а) Для промышленного получения аммиака используется процесс Габера:
Азот получают из воздуха. Водород получают из воды и метана.
б) Первые семь стадий современного процесса Габера предназначены для получения синтез-газа Синтез этой газовой смеси осуществляется на 8-й стадии. Для этого используется железный катализатор. Оптимальный выход и производительность достигаются при температуре 400 °С и давлении 250 атм.
в) Аммиак используется для получения удобрений, азотной кислоты и многих других продуктов.
2. а) Для промышленного получения серной кислоты в настоящее время используется контактный процесс, состоящий из трех стадий.
1-я стадия: получение
2-я стадия: превращение диоксида серы в триоксид серы
Это превращение осуществляется с помощью катализатора, в качестве которого используется оксид . Процесс проводится под давлением, несколько превышающим 1 атм, и при температуре 400 °С.
3-я стадия. Это стадия поглощения. Триоксид серы поглощается 8-ной серной кислотой, образуя олеум, т. е. 99,5%-ную серную кислоту. Затем олеум разбавляют до 98%-ной серной кислоты. Этот процесс можно представить уравнением
б) На заводе контактной серной кислоты с двойным поглощением поглощение триоксида серы осуществляется в две стадии. Промежуточное поглощение осуществляется на 2-й стадии процесса, а окончательное поглощение на 3-й стадии.
в) Серная кислота используется для получения удобрений, красок, синтетических моющих средств, искусственных тканей и многих других продуктов.
Возможно, будет полезно почитать:
- Патриарх кирилл запретил актеру и священнику ивану охлобыстину служить в церкви Охлобыстин церковный сан ;
- Иван охлобыстин - биография, информация, личная жизнь Почему охлобыстин ушел из священников ;
- Ужин для ребенка 4 лет рецепты меню ;
- Принципы функционирования бюджетной системы РФ ;
- Особенности размещения населения на территории земли Население земли размещается равномерно средняя плотность населения ;
- Тонька-пулеметчица — cтрашная судьба страшного человека Фильм палач тонька пулеметчица реальная история ;
- Как поздравить начальницу с юбилеем? ;
- Российские студенты выиграли чемпионат мира по программированию Вот они, герои ;